
A company town is a place where all or most of the stores and housing in the town are owned by the same company that is also the main employer. Company towns are often planned with a suite of amenities such as stores, houses of worship, schools, markets, and recreation facilities.
Some company towns were established to improve living conditions for workers, but many have been regarded as controlling and/or exploitative. Others were not planned, such as Summit Hill, Pennsylvania, United States, one of the oldest, which began as a Lehigh Coal & Navigation Company mining camp and mine site nine miles (14.5 km) from the nearest outside road.
Overview
Traditional settings for company towns were where extractive industries – coal, metal mines, lumber – had established a monopoly franchise. Dam sites and war-industry camps founded other company towns. Since company stores often had a monopoly in company towns, it was frequently possible to pay in scrip through a truck system. However, not all company towns engaged in this particular practice. In the Soviet Union, there were several cities of nuclear scientists (atomics) known as atomgrad; particularly in Ukraine, those were Pripyat, Varash, Pivdennoukrainsk among others.
Typically, a company town is isolated from neighboring towns and centered on a large production factory, such as a lumber or steel mill or an automobile plant. The citizens of the town either work in the factory, work in one of the smaller businesses, or are family members of someone who does. The company may also operate parks, host cultural events such as concerts, donate a church building to a local congregation, etc.
A town that existed before establishing a primary business may not officially be a company town. Still, if a single company employs most citizens, similar conditions may exist (especially regarding the town's economy). Similar dependencies may exist in specific neighborhoods or areas within larger cities.
Company towns often become regular (public) cities and towns as they grow and attract other settlements, business enterprises, and public transportation and services infrastructure. However, if the primary company experiences hardship or fails outright, or the industry fades in importance—such as when anthracite mining declined due to dependence on steam locomotives to spur demand—the economic effect on the company town can be devastating. Without a source of employment, the communities lose property value and population as people leave to find work elsewhere.
History
Paternalism
Paternalism, a subtle form of social engineering, refers to the control of workers by their employers who seek to force middle-class ideals upon their working-class employees. Many nineteenth-century business people considered paternalism as a moral responsibility, or often a religious obligation, which would advance society while furthering their business interests. Accordingly, the company town offered a unique opportunity to achieve such ends.
Although many prominent examples of company towns portray their founders as "capitalists with a conscience", for example, George Cadbury's Bournville, if viewed cynically, the company town was often an economically viable ploy to attract and retain workers. Additionally, for-profit shops within company towns were usually owned by the company, which was unavoidable to its isolated workers, thus resulting in a monopoly for the owners.
Although economically successful, company towns sometimes failed politically due to lacking elected officials and municipally owned services. Accordingly, workers often had no say in local affairs, and therefore felt dictated to. Ultimately, this political climate caused resentment amongst workers and resulted in many residents losing long-term affection for their towns; such was the case at Pullman.
Pullman lesson

Although many small company towns existed in mining areas of Pennsylvania before the American Civil War, one of the most significant and most substantial early company towns in the United States was Pullman, developed in the 1880s just outside the Chicago city limits. The entirely company-owned town provided housing, markets, a library, churches, and entertainment for the 6,000 company employees and an equal number of dependents. Employees were not required to live in Pullman, although workers tended to get better treatment if they chose to live there.
The town operated successfully until the economic panic of 1893 when demand for the company's products declined, and Pullman lowered employee wages and hours to offset the decrease in demand. Despite this, the company refused to lower rents in the town or the price of goods at its shops, thus resulting in the Pullman Strike of 1894. A national commission formed to investigate the causes of the strikes found that Pullman's paternalism was partly to blame and labeled it "Un-American". The report condemned Pullman for refusing to negotiate and for the economic hardships he created for workers in the town of Pullman. "The aesthetic features are admired by visitors, but have little money value to employees, especially when they lack bread." The State of Illinois filed suit, and in 1898, the Supreme Court of Illinois forced the Pullman Company to divest ownership in the town, which was annexed to Chicago.
However, government observers maintained that Pullman's principles accurately provided his employees with a quality of life otherwise unattainable. Still, they recognized that his excessive paternalism was inappropriate for a large-scale corporate economy and thus caused the town's downfall. Accordingly, government observers and social reformers alike saw the need for a balance between control and well-designed towns, concluding that a model company town would only succeed if independent professionals, acting as a buffer between employers and employees, took a role in conception, planning, and management of these towns.
Historian Linda Carlson argues that the managers of corporate towns in the early 20th century believed they could avoid the mistakes made by George Pullman in the 1880s. She says they:
- wanted to create a better life for their employees: decent housing, good schools, and a "morally uplifting" society. In return, they expected stable, hard-working employees who would eschew the evils of drink and, most importantly, not fall prey to the blandishments of union organizers.
Thus, the Pullman Strike did not kill the company town concept but rather initiated a new chapter in their existence. Over the next thirty years, the old model of paternalism was abandoned in favour of new professionally designed company towns with architects, landscape architects, and planners translating "new concepts of industrial relations and social welfare into new physical forms". This suited capitalists of the day who were keen to avoid the experiences of Pullman. The first real example occurred at Indian Hill-North Village, Massachusetts, in 1915.
Decline of American company towns
By the 1920s, the need for company towns had declined significantly due to increased national affluence. Despite income inequalities and a relatively low standard of living conditions amongst factory laborers, the prosperity of the 1920s saw workers' material well-being improve significantly. A strong post-war American economy meant installment buying was accessible to low-wage earners who could now purchase previously unattainable goods like automobiles and radios. Moreover, workers were no longer dependent on employers for healthcare and education.
By the 1920s, widespread ownership of automobiles meant workers no longer needed to live near their workplaces and now had access to more employment opportunities. A combination of the freedom that came with private transport and the mass communication of radio saw the isolation of company towns lessen, and the social basis of the company town became less necessary.
Furthermore, the accessibility of private transport to the working class was a step toward equality, as private transport had previously only been accessible to the wealthy. As access to surrounding municipalities increased, residents of company towns gained access to an increasing amount of government-funded public resources such as schools, libraries, and parks. Accordingly, there was no longer a need for the amenities of company towns which, before welfare capitalism, had previously been unattainable to the working class.
This new-found freedom saw a change in the mindset of workers, who began to look at welfare capitalism as demeaning rather than an incentive. Accordingly, many employees started to request additional pay instead of welfare programs. This was well received by some employers as the idea of 'laissez-faire' individualism, which promoted entrepreneurial virtues of hard work being rewarded rather than direct charity, began to shape new-age paternalism.
Modernization and the increase in material well-being had also lessened the perceived need for paternalism and moral reform. Consequently, the economic downturn of the early 1930s saw some businesses do away with employee welfare schemes to reduce costs. However, the Roosevelt administration's New Deal dealt the final blow to end American company towns by raising minimum wages, encouraging industrial self-governance, and pushing for the owners of company towns to "consider the question of plans for eventual employee ownership of homes". To a lesser extent the New Deal also reduced the need for employee housing by transforming housing finance to a lower-interest, lower-deposit system, making homeownership more accessible to the working class.
Model company towns

During the late nineteenth century, model company towns materialized as enlightened industrialists recognized that many poor workers were living in appalling conditions. These industrialists wished to combat the unsanitary and congested conditions common to working-class districts to create better living conditions for workers. Model company towns such as Port Sunlight (1888) and Bournville (1895) were influential in regards to their building and planning innovation. The ideas generated from these model towns are regarded as having a significant influence on the Garden City movement.
The model company town is concerned with creating a productive and prosperous company. Enlightened industrialists believed this could be achieved by providing a healthier residential environment for their employees. Planning a model company town involved the fusion of new notions of house design and layout. The paternalism of the enlightened industrialist was exhibited in his desire to provide an environment for his employees that was aesthetically appealing and which included well-designed residences, parks, schools, libraries, and meeting halls. The industrialist also wished to contribute to his workers' well-being by providing social programs such as sporting events and functions. This, however, highlights the power and immense control possessed by the company owner, who could shape the lifestyle and activities of his employees to serve his interests and those of the company.
Model villages for agricultural workers were founded in the early 19th century in the United Kingdom. The creation of model company towns was particularly evident in Britain during the latter half of the nineteenth century with the creation of Saltaire (1851), Bournville, Port Sunlight, Creswell and New Earswick (1901) and coincided with the housing-reform movement, which emphasized the improvement of housing for the working class. These model towns contrasted with the overcrowded conditions in British working-class districts, which were often characterized by congested housing, unsanitary conditions, and poor provision of open space and facilities. Model company towns promoted the idea of orderly, planned town development as well as the notion of preparing for the needs of the community to provide healthier living conditions.
Model company towns in Britain
Model company towns around the mid-nineteenth century, such as Copley (1849), near Halifax, and Saltaire (1853), close to Bradford, had improved dwellings for workers, which contrasted with working-class housing in other industrial villages and cities. These model company towns prompted the creation of others, such as Port Sunlight, Bournville, and Creswell, within an environment of reform.
Port Sunlight (1888) in Cheshire was established by William Hesketh Lever (later Lord Leverhulme) of Lever Brothers – a soap and tallow manufacturer. The earlier layout of this model company town was planned to suit the site's undulating topography. Port Sunlight catered for the Lever Brothers employees with improved housing (cottages of varying designs and materials) and gardens, as well as social and community facilities, including an auditorium, a school, tennis courts, and bowling greens. Port Sunlight combined the use of formal and informal planning elements, such as straight streets close to the town centre and curved streets in the residential areas. This combination of the formal and informal represented a new feature of British town planning.
Bournville (1895), near Birmingham, was established by the Cadbury brothers, George and Richard. George and Richard Cadbury chose to transfer the Cadbury factory to this new site to provide their employees with improved living conditions and a country environment that they could enjoy – a far cry from Birmingham's busy, smoky city centre. The firm provided education as a compulsory academic course, and workers were allowed to complete commercial or technical training. The Cadburys also encouraged their workers to get involved in the social life of Bournville by providing sports facilities, athletic and cultural clubs, and social events such as summer parties. George Cadbury, a Quaker, preached Christian values, such as respectability, thrift, and sobriety, and sought to unify the Bournville community through rituals such as gift-giving between employer and employee. The firm also established work councils, such as the Women's Works Council, and supported trade unions.
Bournville represented the union of industry and nature as the company town boasted the attractiveness of the countryside and low-density development with well-built and visually appealing dwellings. Unlike Port Sunlight, Bournville catered for a mixed community, where residences were not restricted to the workforce only. Bournville illustrated how, towards the end of the nineteenth century, low-density development was being punctuated along with the provision of open air, space, and sunlight.Bournville's gardens, parks, tree-lined streets, sense of spaciousness, and country setting enhanced its aesthetic appeal and demonstrated George Cadbury's endeavour to provide workers with a healthy, beautiful, and well-ventilated environment.
The Bolsover Company developed two exemplary mining communities in Derbyshire during the late nineteenth century: Bolsover (1891) and Creswell (1896). The Bolsover Company aimed to provide improved living conditions for the miners and their families in these model industrial villages. The houses at Creswell were built in concentric circles, and within these circles was a large open parkland and a bandstand. Not only did the Bolsover Company aim to provide better housing, but they also wished to improve workers' moral fibre, believing that the provision of facilities and the promotion of workers' welfare would discourage drunkenness, gambling, and bad language. The Bolsover Company provided facilities deemed beneficial for employees at both villages, including clubhouses, bowling greens, cooperative society stores, cricket pitches, and schools. During the early years of these model industrial villages, the Bolsover Company organized various events intended to enhance community life, such as flower shows, lectures, sporting events, concerts, teas, and dances.
Industrial colonies in Catalonia

Catalonia, located in north-eastern Spain, has an especially high density of company towns, known locally as industrial colonies. They are especially concentrated in river basins along the Ter and Llobregat and their tributaries. In Berguedà, for example, within 20 km, there are 14 colonies. The total number in Catalonia is around a hundred. These were small towns created around a factory or mine, built in a rural area, and, therefore, separate from any other population. They typically housed between 100 and 500 inhabitants; in some cases, upwards of 1000 people lived in these towns.
These industrial colonies were an emblematic aspect of industrialization in Catalonia, specifically, the second industrialization, which resulted in certain areas that were once purely rural becoming industrial. They were first created in the second half of the nineteenth century, especially in the 1870s after the American Civil War ended and raw cotton again became readily available. The last colonies were created in the early years of the twentieth century. Thus, company towns in Catalonia have a history going back some 150 years; however, in almost all cases, the company that operated the colony has now shut down. The most common industry in these colonies was textiles, and the most important from the standpoint of architecture, urban design, and the complexity of their operation. More than 75 textile colonies were recorded, although there were also mining, metallurgy, cement, and agricultural colonies.
These colonies (particularly the textile-related ones) were mostly constructed close to a river. This was because they used hydraulic power (waterwheels) to run the factory. One reason for this was that Catalonia was poor in coal, and importing it was expensive. In addition, the Catalan rivers (with little volume but a very steep sloping run) provided free and almost inexhaustible energy, which was lacking only in times of drought.
The industrial colonies' system began to collapse in the 1960s due to their inflexible capital structure and social changes, such as the desire for workers to own appliances, cars, or homes, the declining influence of religion, and the opportunities offered by towns. The colonies gradually emptied of people even before the definitive industrial crisis, which worsened in 1978. In the 1980s and 1990s, almost all the factories in these industrial colonies closed. From that moment on, many colonies became towns that were now independent of the company, others were abandoned and remain without inhabitants. Other factories were leased to smaller industries or now lie empty.
Some of the more interesting colonies include: Colònia Güell, in Santa Coloma de Cervelló, which contains several modernist buildings, such as the crypt church built by Antoni Gaudí; L'Ametlla de Merola, Puig-reig, where centenary traditional cultural activities are held, such as the representation of Els Pastorets; the three colonies of Castellbell i el Vilar: La Bauma, El Borràs, El Burés, with buildings of architectural interest; Cal Rosal, between Berga, Avià and Olvan, which, in 1858, was the first colony in the era of building large colonies in the Llobregat; Cal Vidal, Puig-reig, which houses the Museum of the Vidal Colony, or the Museum of the Sedó Colony, ideal visits for anyone wishing to learn what life was like in one of these industrial experiments.
Examples
Belgium

Having bought the mining concession of Grand-Hornu in 1810, French industrialist Henri De Gorge soon realized the need to accommodate the growing workforce of his expanding business. He commissioned architect François Obin and, after his death, Bruno Renard, to build a functional complex in a neoclassical style. Grand-Hornu became one of the world's first purpose-built company towns. It was abandoned in 1954 after the mine was closed. It currently houses a museum of contemporary art and temporary exhibitions. Grand-Hornu is one of the four industrial sites in Wallonia that were listed by UNESCO as a World Heritage Site in 2012.
Brazil
Fordlândia was established by American industrialist Henry Ford in 1928 as a prefabricated industrial town in the Amazon rainforest of Brazil. It was intended to be inhabited by 10,000 people, but it failed, and the city was abandoned in 1934.
Canada

Arvida, Quebec was developed in 1927 as a company town. The town grew to have a population of about 14,000 inhabitants, four Catholic parishes, and many other denominations, parishes, and schools. It was known as "the City Built in 135 Days".
Batawa was set up by the Bata Shoe Company as a planned community around a shoe factory. The factory opened in 1939 and closed in 2000.
Chile
Two of Chile's UNESCO World Heritage Sites correspond to former company towns.
Humberstone was a settlement dedicated to the extraction of saltpeter during said commodity's boom in the late 19th and early 20th centuries. The town was founded and administered by James Thomas Humberstone's Peru Nitrate Company, later acquired by Compañía Salitrera de Tarapacá y Antofagasta (COSATAN), before turning into a ghost town by the 1960s due to the steady decline in the global price of nitrates caused by the development of chemically engineered fertilizers.
Sewell was a mining town intended as both a residential and industrial hub linked to the nearby El Teniente copper mine. Founded in 1906 by the Braden Copper Company, it came to house over 16,000 inhabitants at its peak despite its remote location on the slopes of the Andes. The problematic geography on which the town was erected led to its distinctive appearance, with steep staircases and no streets for vehicular access. Although the El Teniente mine remains active, the town itself began to be dismantled and abandoned by the late 1960s as the maintenance of a remote on-site town was no longer financially viable. Some industrial activities still occur on Sewell's grounds, but workers have primarily been relocated to nearby urban centres.
Finland
Kuusankoski in Finland, formerly also known as "the paper capital of Finland", is a prime example of the decline many company towns have had to deal with when the company itself struggles. The town relied on three paper mills owned by Kymmene Corporation from the 1870s until 2005, when two mills, Voikkaa and Kuusaa, were shut down, leaving only the Kymi mill operating. The two closed mills employed an estimated 5% of the local population, and Kymmene's decision left the town in socioeconomic chaos. Kuusankoski's independent status ended in 2009 when the town was consolidated into Kouvola's regional capital.
France
The French city of Le Creusot is a company town.
Germany
Leverkusen was founded in 1861 around Carl Leverkus' dye factory that later became the headquarters of Bayer. The city of Ludwigshafen has been dominated by BASF's plants since the chemical company moved here in 1865. The neighboring municipality Limburgerhof also emerged from housing estates for BASF workers. Neuölsburg, built since 1875 for the workers of Ilseder Hütte, was a separate municipality until 1964. Many other companies, especially in the mining and steel industry, built housing estates for their workers near existing cities rather than separate company towns. A notable example is Siedlung Eisenheim in Oberhausen from the mid-19th century, once home to 1200 steel smelters of the Gutehoffnungshütte, which is now protected as a historic monument. The mining settlements built around the coal pits of the Ruhr region were called Zechenkolonien ("pit colonies").
Wolfsburg was created as a planned city in 1938 to host the Volkswagen plant and its workers. A similar Nazi-era planned town is Salzgitter, built around the Reichswerke Hermann Göring that later became the Salzgitter AG. In 1950s East Germany, Eisenhüttenstadt ("ironworks city", initially Stalinstadt) was built from scratch, housing the workers of the Eisenhüttenkombinat Ost ironworks.
Japan

In Japan, an equivalent to company towns are "Kigyō Jōkamachi" (企業城下町 , Company castle town). However, these differ from company towns because the companies do not own or develop them. Instead, the term refers to towns where a specific company has a major influence on the town's economy due to that company or its subcontractors employing a significant part of the town's population. An example is Toyota, Aichi (豊田市), where the "castle" company is the automobile manufacturer Toyota. In some cases, such towns can be named after the company. For example, Toyota City changed its name from Koromo City and named the area of the town where Toyota's headquarters is situated "Toyota-machi " (トヨタ町, note that katakana is used here to reflect the company name) in 1959.
Mexico
During the Porfiriato, American-owned mining towns that settled areas mostly uninhabited areas included Cananea, El Boleo, Nacozari, Navojoa, Copala, Concordia, Santa Eulalia, Santa Rosalía de Camargo, Batopilas, and Esperanzas. Americans and Mexicans were segregated, with the 1906 Cananea strike precipitating the Mexican Revolution.
Namibia
Oranjemund was privately owned by De Beers until 2017 and thus governed by the diamond mining company's administration. In 2011, the political administration was handed over to the government, which proclaimed it a town. It is now governed by a seven-seat town council.
During South African Apartheid, a form of company towns existed under the contract labor system in Namibia, then South West Africa, a colony of South Africa. Indigenous workers were coerced into signing yearlong contracts in caged-in factory compounds, which they were not allowed to leave without permission, with movement strictly controlled by Pass laws. In addition they lived in the compound dorms and primarily got food from the compound's cafeteria, both under the control of their employers. As such, alongside the typically bad working conditions, it has been characterized by many as close to slavery.
Poland
Widzew, a suburb of Łódź in Poland, had been a textile company town before the Second World War.
Slovakia
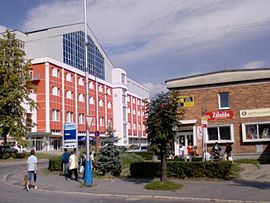
Svit in Slovakia was founded in 1934 by business industrialist Jan Antonín Baťa following his policy of establishing well-organized model communities for his workers and other employees. This town (like other Baťa's company towns) was also an example of social engineering.
Sweden
The mining city of Kiruna in Sweden was originally around 1900, built by the mining company in an unpopulated area. Many buildings, including the church, were built by the company. Many smaller towns were built and even planned by companies. Skoghall in Värmland is such an example where Stora AB owned a papermill and contained a city-planning office.
Ukraine
The city of Pripyat in Ukraine was established in 1970 solely to house the workers at the adjacent Chernobyl Nuclear Power Plant and their families. It was one of several "nuclear cities" constructed by Soviet nuclear power firms throughout the latter half of the 20th century. All amenities, stores, and employment were conducted through each nuclear city's power plant administration.
United States

At their peak, there were more than 2,500 company towns, housing 3% of the US population.
The rate of company owned housing however was higher, the Bureau of Labor Statistics surveyed a sample of 213 companies for 1916, a full 34.4% of their workforce lived in company housing. However, the survey covered primarily manufacturing (textile, iron & steel mills) and mining towns.
The companies that ran the towns were mainly labor-intensive companies such as coal, steel, lumber, and various war industries. Most people living in these towns were immigrants new to the country. The tight, paternalistic control exerted by companies over the residents' behavior and even opinions caused issues and concerns.

Segundo, Colorado, was a company town where the CF&I coal company housed its workers. It offered adequate housing and promoted upward mobility through its sponsorship of a YMCA Center, an elementary school, some small businesses, and a company store. However, air pollution was a constant health threat, and the houses lacked indoor plumbing. As demand for metallurgical coal declined, the mine laid off workers, and Segundo's population declined. After a major fire in 1929, CF&I left town, and Segundo became a ghost town.
One famous company town was McDonald, Ohio, which was created by the Carnegie Steel Company to house and serve the needs of its employees in the Youngstown, Ohio, area.
Marktown, Clayton Mark's planned worker community, was an example in northwest Indiana.
In the present-day United States, it is relatively rare for any place in which a single company owns all the property to be granted status as an incorporated municipality. Instead, companies prefer their wholly owned communities to remain unincorporated, as this permits community administration to be carried out by appointed company officers rather than elected officials. However, incorporated municipalities heavily depend upon a single industry or organization and may be loosely considered a "company town", even though the company does not technically own the town.
Scotia, California is a company town, previously owned by The Pacific Lumber Company, and is being dismantled through PLC's bankruptcy process.
Cass, West Virginia, is a former company town now a state park. Originally founded in 1901, the town of Cass served employees who cut and processed lumber from the surrounding mountain slopes. Some of the remaining houses are available for rental; other features are the company store and an operating railway.
Bay Lake, Florida and Lake Buena Vista, Florida are controlled by The Walt Disney Company.
Bryce Canyon City, Utah is a current company town incorporated in 2007, consisting solely of Ruby's Inn's property and its third-generation owners, the Syrett family.
In 2021, the governor of Nevada, Steve Sisolak, announced a plan to launch so-called "Innovation Zones" in Nevada to attract technology firms. The zones would permit companies with large land areas to form governments with the same authority as counties, including imposing taxes, forming school districts and courts, and providing government services. The measure to further economic development with the "alternative form of local government" has not yet been introduced in the Legislature. Sisolak pitched the concept in his State of the State address on January 19. By allowing tech corporations to establish their governments, the plan is hoped to bring in new businesses at the forefront of "groundbreaking technologies" without the state cutting taxes or paying economic rent that previously helped Nevada attract companies like Tesla Inc.
In March 2021, Elon Musk announced plans to incorporate the Boca Chica area of far southeastern Texas, the site of a SpaceX rocket manufacturing and launch facility, as the city of "Starbase". Some have labeled the plans and SpaceX's existing operations in the area as an example of a company town.