Why do costs exceed projections?
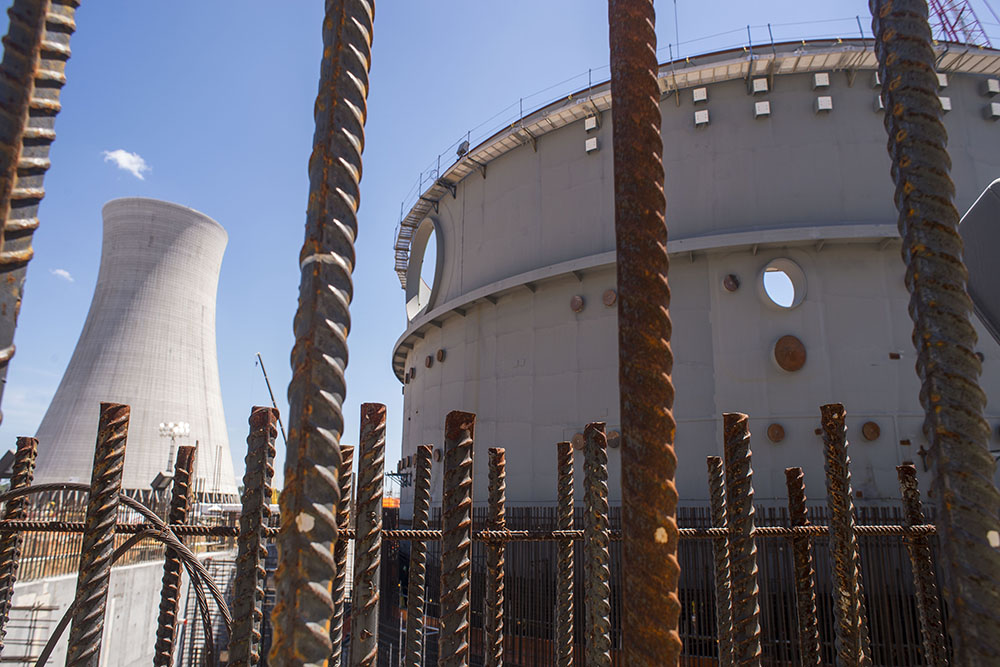
In brief
An MIT team has revealed why, in the field of nuclear power, experience with a given technology doesn’t always lower costs. When it comes to building a nuclear power plant in the United States—even of a well-known design—the total bill is often three times as high as expected. Using a new analytical approach, the researchers delved into the cost overrun from non-hardware-related activities such as engineering services and labor supervision. Tightening safety regulations were responsible for some of the cost increase, but declining labor productivity also played a significant role. Analyses of possible cost-reduction strategies show potential gains from technology development to reduce materials use and to automate some construction tasks. Cost overruns continue to be left out of nuclear industry projections and overlooked in the design process in the United States, but the researchers’ approach could help solve those problems. Their new tool should prove valuable to design engineers, developers, and investors in any field with demanding and changeable regulatory and site-specific requirements.
Nuclear power is frequently cited as a critical component in the portfolio of technologies aimed at reducing greenhouse gas emissions. But rising construction costs and project delays have hampered efforts to expand nuclear capacity in the United States since the 1970s. At plants begun after 1970, the average cost of construction has typically been far higher than the initial cost estimate.
Nevertheless, the nuclear industry, government, and research agencies continue to forecast cost reductions in nuclear plant construction. A key assumption in such projections is that costs will decline as the industry gains experience with a given reactor design. “It’s often included in models, with huge impacts on the outcomes of projected energy supply mixes,” says Jessika E. Trancik, an associate professor of energy studies in the MIT Institute for Data, Systems, and Society (IDSS).
That expectation is based on an assumption typically expressed in terms of the “learning rate” for a given technology, which represents the percent cost reduction associated with a doubling of cumulative production. Nuclear industry cost-estimating guidelines as well as widely used climate models and global energy scenarios often rely on learning rates that significantly reduce costs as installed nuclear capacity increases. Yet empirical evidence shows that in the case of nuclear plants, learning rates are negative. Costs just keep rising.
To investigate, Trancik and her team—co-first authors Philip Eash-Gates SM ’19 and IDSS postdoc Magdalena M. Klemun PhD ’19; IDSS postdoc Gökşin Kavlak; former IDSS research scientist James McNerney; and TEPCO Professor of Nuclear Science and Engineering Jacopo Buongiorno—began by looking at industry data on the cost of construction (excluding financing costs) over five decades from 107 nuclear plants across the United States. They estimated a negative learning rate consistent with a doubling of construction costs with each doubling of cumulative U.S. capacity.
That result is based on average costs across nuclear plants of all types. One explanation is that the rise in average costs hides trends of decreasing costs in particular reactor designs. So the researchers examined the cost trajectories of four standard plant designs installed in the United States that reached a cumulative built capacity of 8 gigawatts-electric. Their results appear below. They found that construction costs for each of the four designs rose as more plants were built. In fact, the first one built was the least expensive in three of the four cases and was among the least expensive plants in the fourth.
“We’ve confirmed that costs have risen even for plants of the same design class,” says Trancik. “That outcome defies engineering expectations.” She notes that a common view is that more stringent safety regulations have increased the cost of nuclear power plant construction. But is that the full explanation, or are other factors at work as well?
Source of increasing cost
To find out, the researchers examined cost data from 1976 to 1987 in the U.S. Department of Energy’s Energy Economic Data Base. (After 1987 the DOE database was no longer updated.) They looked at the contributions to overall cost increases of 61 “cost accounts” representing individual plant components and the services needed to install them.
They found that the overall trend was an increase in costs. Many accounts contribute to the total cost escalation, so the researchers couldn’t easily identify one source. But they could group the accounts into two categories: direct costs and indirect costs. Direct costs are costs of materials and labor needed for physical components such as reactor equipment and control and monitoring systems. Indirect costs are construction support activities such as engineering, administration, and construction supervision. The figure below shows their results.
The researchers concluded that between 1976 and 1987, indirect costs—those external to hardware—caused 72% of the cost increase. “Most aren’t hardware-related but rather are what we call soft costs,” says Trancik. “Examples include rising expenditures on engineering services, on-site job supervision, and temporary construction facilities.”
To determine which aspects of the technology were most responsible for the rise in indirect expenses, they delved further into the DOE dataset and attributed the indirect expenses to the specific plant components that incurred them. The analysis revealed that three components were most influential in causing the indirect cost change: the nuclear steam supply system, the turbine generator, and the containment building. All three also contributed heavily to the direct cost increase.
A case study
For further insight, the researchers undertook a case study focusing on the containment building. This airtight, steel-and-concrete structure forms the outermost layer of a nuclear reactor and is designed to prevent the escape of radioactive materials as well as to protect the plant from aircraft impact, missile attack, and other threats. As such, it is one of the most expensive components and one with significant safety requirements.
Based on historical and recent design drawings, the researchers extended their analysis from the 1976–1987 period to the year 2017. Data on indirect costs aren’t available for 2017, so they focused on the direct cost of the containment building. Their goal was to break down cost changes into underlying engineering choices and productivity trends.
They began by developing a standard cost equation that could calculate the cost of the containment building based on a set of underlying variables—from wall thickness to laborer wages to the prices of materials. To track the effects of labor productivity trends on cost, they included variables representing steel and concrete “deployment rates,” defined as the ratio of material volumes to the amount of labor (in person-hours) required to deploy them during construction.
A cost equation can be used to calculate how a change in one variable will affect overall cost. But when multiple variables are changing at the same time, adding up the individual impacts won’t work because they interact. Trancik and her team therefore turned to a novel methodology they developed in 2018 to examine what caused the cost of solar photovoltaic modules to drop so much in recent decades. Based on their cost equation for the containment building and following their 2018 methodology, they derived a “cost change equation” that can quantify how a change in each variable contributes to the change in overall cost when the variables are all changing at once.
Their results, summarized in the right-hand panel of the figure below, show that the major contributors to the rising cost of the containment building between 1976 and 2017 were changes in the thickness of the structure and in the materials deployment rates. Changes to other plant geometries and to prices of materials brought costs down but not enough to offset those increases.
Percentage contribution of variables to increases in containment building costs These panels summarize types of variables that caused costs to increase between 1976 and 2017. In the first time period (left panel), the major contributor was a drop in the rate at which materials were deployed during construction. In the second period (middle panel), the containment building was redesigned for improved safety during possible emergencies, and the required increase in wall thickness pushed up costs. Overall, from 1976 to 2017 (right panel), the cost of a containment building more than doubled.
As the left and center panels above show, the importance of those mechanisms changed over time. Between 1976 and 1987, the cost increase was caused primarily by declining deployment rates; in other words, productivity dropped. Between 1987 and 2017, the containment building was redesigned for passive cooling, reducing the need for operator intervention during emergencies. The new design required that the steel shell be approximately five times thicker in 2017 than it had been in 1987—a change that caused 80% of the cost increase over the 1976–2017 period.
Overall, the researchers found that the cost of the reactor containment building more than doubled between 1976 and 2017. Most of that cost increase was due to increasing materials use and declining on-site labor productivity—not all of which could be clearly attributed to safety regulations. Labor productivity has been declining in the construction industry at large, but at nuclear plants it has dropped far more rapidly. “Material deployment rates at recent U.S. ‘new builds’ have been up to 13 times lower than those assumed by the industry for cost estimation purposes,” says Trancik. “That disparity between projections and actual experience has contributed significantly to cost overruns.”
Discussion so far has focused on what the researchers call “low-level mechanisms” of cost change—that is, cost change that arises from changes in the variables in their cost model, such as materials deployment rates and containment wall thickness. In many cases, those changes have been driven by “high-level mechanisms” such as human activities, strategies, regulations, and economies of scale.
The researchers identified four high-level mechanisms that could have driven the low-level changes. The first three are “R&D,” which can lead to requirements for significant modifications to the containment building design and construction process; “process interference, safety,” which includes the impacts of on-site safety-related personnel on the construction process; and “worsening despite doing,” which refers to decreases in the performance of construction workers, possibly due to falling morale and other changes. The fourth mechanism— “other”—includes changes that originate outside the nuclear industry, such as wage or commodity price changes. Following their 2018 methodology, the team assigned each low-level cost increase to the high-level mechanism or set of mechanisms that caused it.
The analysis showed that R&D-related activities contributed roughly 30% to cost increases, and on-site procedural changes contributed roughly 70%. Safety-related mechanisms caused about half of the direct cost increase over the 1976 to 2017 period. If all the productivity decline were attributed to safety, then 90% of the overall cost increase could be linked to safety. But historical evidence points to the existence of construction management and worker morale issues that cannot be clearly linked to safety requirements.
Lessons for the future
The researchers next used their models in a prospective study of approaches that might help to reduce nuclear plant construction costs in the future. In particular, they examined whether the variables representing the low-level mechanisms at work in the past could be addressed through innovation. They looked at three scenarios, each of which assumes a set of changes to the variables in the cost model relative to their values in 2017.
In the first scenario, they assume that cost improvement occurs broadly. Specifically, all variables change by 20% in a cost-reducing direction. While they note that such across-the-board changes are meant to represent a hypothetical and not a realistic scenario, the analysis shows that reductions in the use of rebar (the steel bars in reinforced concrete) and in steelworker wages are most influential, together causing 40% of the overall reduction in direct costs.
In the second scenario, they assume that on-site productivity increases due to the adoption of advanced manufacturing and construction management techniques. Scenario 2 reduces costs by 34% relative to estimated 2017 costs, primarily due to increased automation and improved management of construction activities, including automated concrete deployment and optimized rebar delivery. However, costs are still 30% above 1976 costs.
The third scenario focuses on advanced construction materials such as high-strength steel and ultra-high-performance concrete, which have been shown to reduce commodity use and improve on-site workflows. This scenario reduces cost by only 37% relative to 2017 levels, in part due to the high cost of the materials involved. And the cost is still higher than it was in 1976.
Decreases in containment building costs due to four high-level mechanisms under three innovation strategies Scenario 1 assumes a 20% improvement in all variables; Scenario 2 increases on-site material deployment rates by using advanced manufacturing and construction management techniques; and Scenario 3 involves use of advanced, high-strength construction materials. All three strategies would require significant R&D investment, but the importance of the other high-level mechanisms varies. For example, “learning-by-doing” is important in Scenario 2 because assumed improvements such as increased automation will require some on-site optimization of robot operation. In Scenario 3, the use of advanced materials is assumed to require changes in building design and workflows, but those changes can be planned off-site, so are assigned to R&D and “knowledge spillovers.”
To figure out the high-level mechanisms that influenced those outcomes, the researchers again assigned the low-level mechanisms to high-level mechanisms, in this case including “learning-by-doing” as well as “knowledge spillovers,” which accounts for the transfer of external innovations to the nuclear industry. As shown above, the importance of the mechanisms varies from scenario to scenario. But in all three, R&D would have to play a far more significant role in affecting costs than it has in the past.
Analysis of the scenarios suggests that technology development to reduce commodity usage and to automate construction could significantly reduce costs and increase resilience to changes in regulatory requirements and on-site conditions. But the results also demonstrate the challenges in any effort to reduce nuclear plant construction costs. The cost of materials is highly influential, yet it is one of the variables most constrained by safety standards, and—in general—materials-related cost reductions are limited by the large-scale dimensions and labor intensity of nuclear structures.
Nevertheless, there are reasons to be encouraged by the results of the analyses. They help explain the constant cost overruns in nuclear construction projects and also demonstrate new tools that engineers can use to predict how design changes will affect both hardware- and non-hardware-related costs in this and other technologies. In addition, the work has produced new insights into the process of technology development and innovation. “Using our approach, researchers can explore scenarios and new concepts, such as microreactors and small modular reactors,” says Trancik. “And it may help in the engineering design of other technologies with demanding and changeable on-site construction and performance requirements.” Finally, the new technique can help guide R&D investment to target areas that can deliver real-world cost reductions and further the development and deployment of various technologies, including nuclear power and others that can help in the transition to a low-carbon energy future.